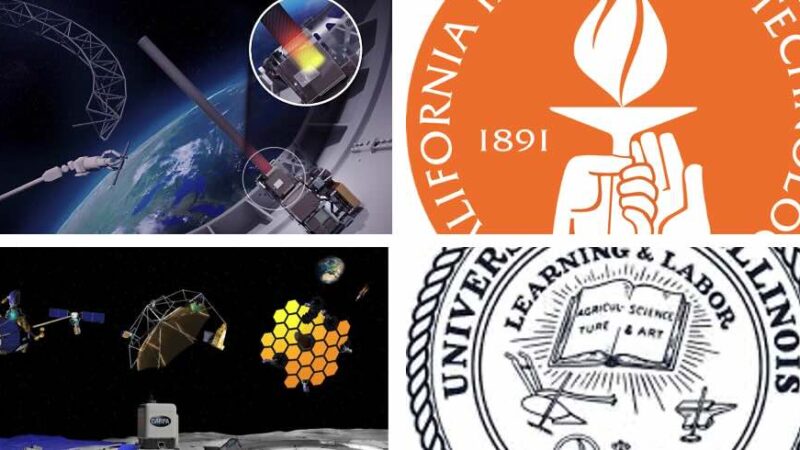
随着在轨制造技术不断取得突破,美国国防高级研究计划局(DARPA)宣布,其“轨道结构材料与制造”计划(Novel Orbital and Moon Manufacturing, Materials, and Mass-efficient Design,简称 NOM4D)将进入全新阶段:由实验室测试转向轨道实地演示《Manufacturing experiment will move from the lab to in-orbit evaluation》。这标志着人类在摆脱火箭整流罩尺寸限制、实现太空中直接构建大型结构方面迈出关键一步。
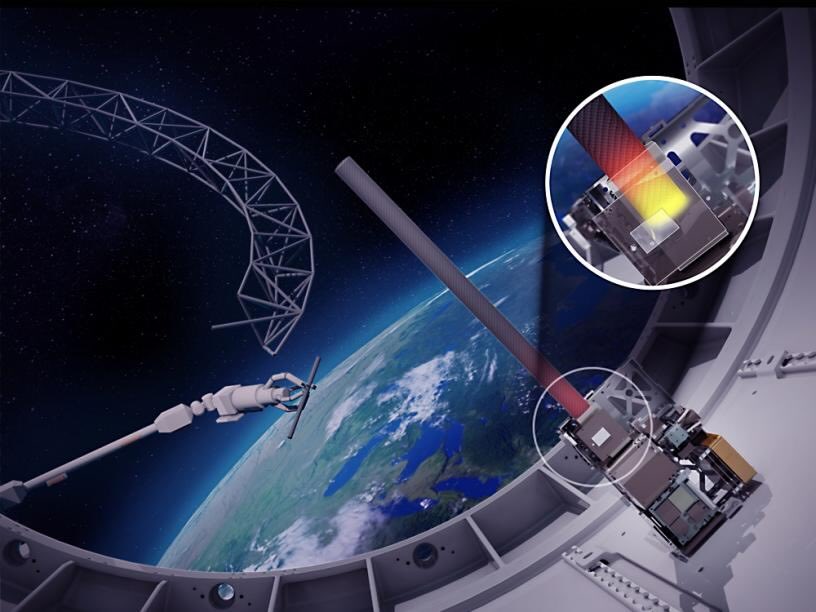
摆脱整流罩束缚,重构太空结构制造范式
目前,所有进入太空的结构仍需压缩折叠,以适应火箭整流罩的有限空间,且为承受发射过程中的巨大加速度和震动,结构设计往往远重于其在轨实际承载需求。这不仅限制了结构尺寸,还大幅降低了质量效率。
为突破这一“整流罩束缚”,DARPA 于2022年启动了NOM4D项目,提出了一种全新的太空建造思路:将不需为发射强化的新型轻质原材料送入轨道,在失重环境中直接进行组装制造。这不仅可以建造远大于整流罩直径的结构,也为开发全新的结构形态提供了可能。
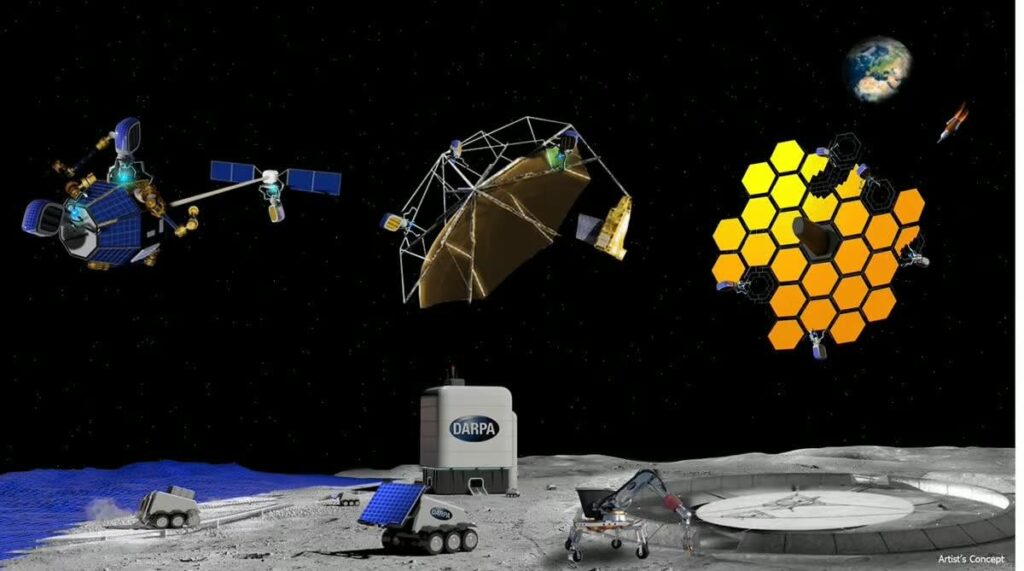
“我们正在从‘在地球制造、在太空部署’,迈向‘在太空制造、为太空而设计’的新范式。”NOM4D 项目负责人 Andrew Detor 表示。
基于前期在材料、结构设计与自动化装配方面的进展,DARPA 宣布将 NOM4D 项目的第三阶段从计划中的地面精度验证,直接升级为两项轨道演示任务。
加州理工学院:机器人自动组装轻质桁架
加州理工团队聚焦于质量效率极高的结构设计。他们与商业太空公司 Momentus 合作,计划于 2026 年2月搭载 SpaceX 猎鹰9号 Transporter-16 任务,将自主组装装置送入低地球轨道,并安装于 Momentus 的 Vigoride 轨道服务飞行器上。
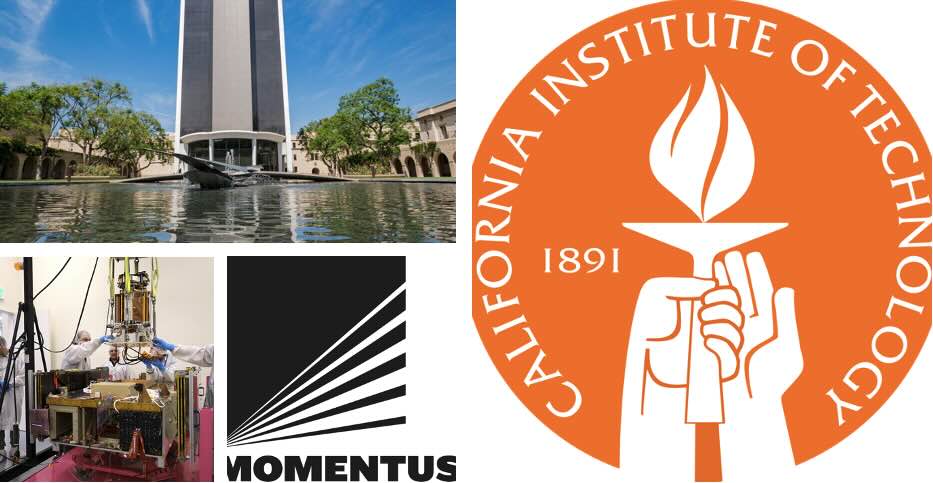
此次演示为全自动“自由飞行”实验,装置无需人工操作,即可在轨通过龙门式机械臂自动拼装出直径1.4米的轻质复合材料桁架结构,模拟空间天线骨架的组装过程。整个过程将通过轨道器自带摄像系统实时拍摄,用以评估组装工艺的可靠性与材料在太空环境中的适应性。
Detor 解释:“这项演示并不会构建真正的射频天线,而是验证机器人是否能够可靠地操作这些细长轻质构件,在轨组装出稳定的框架结构,并完成类似射频反射面材料的悬挂部署。”
伊利诺伊大学厄本那-香槟分校:高精度复合材料在轨固化
伊利诺伊大学团队则专注于先进复合材料的成形技术。他们与 Voyager Space 合作,预计于2026年4月搭载 NASA 的 NG-24 补给任务,将新型材料系统送至国际空间站,并在 Bishop 气闸舱内开展实验。
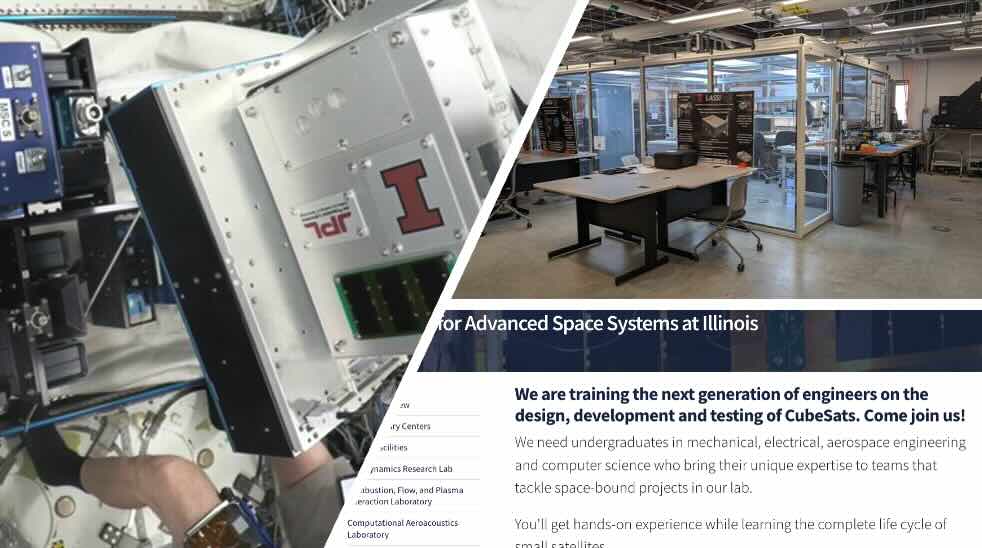
其核心技术为“前沿聚合”(Frontal Polymerization)固化方法:利用一种新开发的碳纤维编织结构,结合特制的液态单体,在不借助高温高压环境的情况下,仅通过在材料一端触发聚合反应,即可沿材料长度方向依次推进固化过程,从而构建高强度碳纤维管材。
“在地球上,我们制造这类复合材料需要高压釜和高温环境。但在太空中,这种可扩展、无需整体加热的固化方法具有革命性意义。”Detor 强调,“这为在轨制造大尺度构件提供了现实路径。”
激光金属成形亦在推进
除了上述两项轨道演示,佛罗里达大学也参与了第三阶段研究。他们致力于利用激光进行金属板材的精密折弯成形,并与 NASA 马歇尔太空飞行中心展开深度合作,探索将金属弯折工艺引入未来的太空制造流程中,与已有的焊接与切割技术形成互补。
为月球轨道与深空构建“制造生态”
随着 NASA 和商业公司加速布局以月球为中心的空间经济,如何在地月空间(Cislunar Space)这一遥远、通信延迟更大的环境中,构建并维护大规模基础设施,已成为商业探索的关键课题。
“我们设想,未来利用 NOM4D 技术,可以在轨制造直径超过100米的射电天线。”Detor 表示,“同时,也为建设如太空加油站、太阳能发电场、月球基地等打下制造能力基础。”
他补充道:“NOM4D 的目标不仅是验证技术本身,更是为建立完整的太空制造生态系统奠定基础。”